DIY algorithm for making a coordinate table for beginners
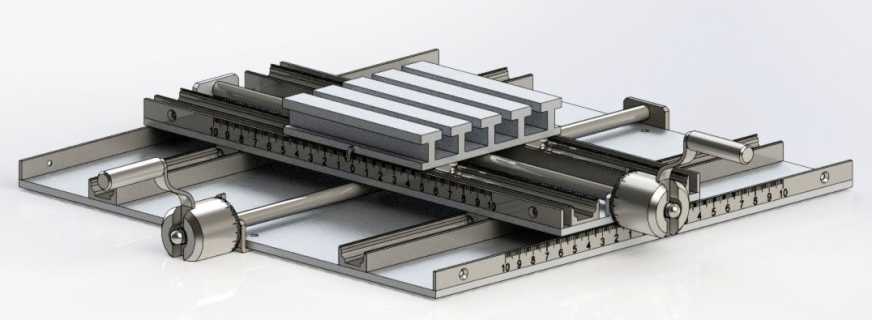
For the proper operation of drilling equipment, several additional devices are needed that will facilitate the work of the master and increase its effectiveness. In particular, a special work surface is needed to equip the machine, increasing the productivity of the device. Making a good coordinate table with your own hands is not so simple, but it is possible. An experienced specialist will assemble it, well saving money on the purchase of factory equipment.
Content
Advantages and disadvantages of self-made
The coordinate table is an additional design to the milling, drilling metal or woodworking machine. Thanks to it, it is possible to increase the productivity of equipment, reducing the complexity of the process of processing parts. The workpiece is simply fixed on the work surface and can smoothly move along a given path.
Homemade coordinate tables have advantages:
- small dimensions;
- simple structural form;
- mechanically controlled;
- used in handicraft production.
Their main advantage is money saving. Making such a design from scratch will be much cheaper than buying a factory manipulator.Of course, there are a number of difficulties in self-manufacturing. We need a suitable drawing, in accordance with which the required trajectory of the workpiece will be set. If someone’s experience is not there, you will have to create it yourself, but any error in drawing the circuit will make itself felt during operation. In addition, a do-it-yourself table is only suitable for small-scale production, since the simplest home-made mechanisms wear out much faster than factory ones.
For serial production of parts and their processing, only the factory model of the coordinate table is suitable.
Design selection
When choosing a design, you need to determine its size. If the equipment processing the part is to be installed on the coordinate table, then its dimensions must be taken into account necessarily. If it is needed to fix the workpiece, it is mounted on the bed of drilling equipment, and in width and length it will be about 35 x 35 cm.
There are tables and the type of mount:
- In the manufacture of a coordinate table with your own hands, the design is equipped with mechanical fastening. This is the simplest solution from the point of view of implementation, but it has several disadvantages.For example, often leads to processing errors, and there is a risk of deformation of the surface of the product.
- Vacuum fasteners are considered the best option. With its help, accurate positioning of the workpiece on a horizontal plane is ensured. When an air stream is fed into the gap between the countertop and the workpiece, the pressure in this area changes. Due to this, it is possible to carry out processing better (without mechanical damage to the product).
- Mounting under the weight of the workpiece is suitable if heavy parts need to be machined when using a drilling machine. Due to its mass, the based product remains in the same place even under strong influence.
The functionality of the table depends on the number of degrees of freedom:
- If it is one, then the workpiece can only be moved in one direction (this is a good option for processing flat products).
- If there are two degrees, it becomes possible to move the workpiece along the X and Y coordinates.
- If there are three of them, then the part can move up, down and along the Z coordinate.
If the table is made for home production and processing of parts, then the use of two degrees of freedom is more than enough.
When making a coordinate table with your own hands, it is important to decide for what purpose it will be used. The parameters of the manipulator are selected in accordance with the dimensions, weight and shape of future workpieces. To work with different parts from metal and wood, a complex multifunctional mechanism is made. Usually, masters at home lack the capabilities of a small-sized table with mechanical fasteners and two degrees of freedom.
Materials and mechanisms of structural elements
The durability of the structure and the cost price depend on the material of the product. It should immediately be decided whether the table will be steel, aluminum or cast iron. The second important step is to decide on the control mechanism. It should also be decided whether the drive should be mechanical or electrical. The third step is to choose the guides. This will affect the accuracy of the workpiece.
Base
The following materials are taken for the basis:
- Cast iron. Expensive, heavy material in operation is very fragile, so it is extremely rarely used in the production of a drilling machine.
- Steel. The material is the highest strength and durable. Its main drawback is the cost. Not every master can purchase it.
- Aluminum. Light and soft material is easier to work with. It is not as expensive as steel. But for the manufacture of a large-sized table it will not work, as it will not withstand the heavy weight of large workpieces. To create mini-equipment, this is an ideal option.
If the master processes metal blanks, it is better to make a table of steel or cast iron. True, you should immediately evaluate your costs: it may be that the purchase of a ready-made manipulator will be cheaper than that of expensive iron. For work with wood or plastic, an aluminum countertop is suitable.
Drive unit
A drive is a control mechanism by which the coordinate table will change its position. It happens:
- Mechanical. It is easiest to make it yourself. It allows you to significantly reduce the cost of the table. A conventional screw or belt drive is taken as the basis - this is enough to establish small-scale production. The mechanics are not able to provide 100% accuracy, and this is its unique disadvantage.
- Electric. It guarantees zero error when performing work operations, however it is very difficult to do it yourself. Often found in factory models of tables. If there is no power source near the workplace, this option will not work.
A separate category of coordinate tables should include models with CNC (numerical program control).This is a high-tech equipment that is used by large enterprises for production in huge volumes. Their main advantages: good performance, as well as full or partial automation of the process. Disadvantages: high cost, for some parts such a drive will not work.
Guides
The accuracy of the workpiece processing depends on these elements, so they need to be selected correctly. Among those that can be done with their own hands, the following are distinguished:
- Rail. Rectangular guides are considered structurally more advanced. When using them, there are less friction losses and avoidance of serious errors. It is possible to connect a lubricant supply system.
- Cylindrical. The use of rounded guides is fraught with high heat due to friction. For machines of the so-called small category, they are suitable, but you will have to lubricate all the mechanisms manually.
Guides are made with a carriage and bearing assemblies. The use of plain bearings will provide high precision machining parts. The use of a rolling shaft support will reduce friction and extend the life of the manipulator.
The rolling bearing can lead to noticeable play, which reduces the accuracy of the workpiece.
A carriage is a block of guides (a mechanism unit) that moves directly along them. It can provide for increased flange dimensions, which allows it to be mounted on the underside of the table. If it is not at all, then the carriage is placed on top (threaded method).
Moving device
Choosing a moving device, you should answer a number of questions:
- What should be the processing speed.
- What positioning accuracy is acceptable when performing work operations.
- How productive equipment will be used.
Belt moving device is used in the manufacture of home-made coordinate tables most often. At a cost it is cost-effective, but it has a number of disadvantages. The belt wears out quickly enough, and can also stretch during operation. In addition, due to its slipping, the accuracy of the movable element is reduced.
Ball screw transmission is a more durable and reliable option. Despite the small dimensions of the device, it has good load capacity, and the movement is carried out evenly and with great accuracy. Smooth and almost silent running, as well as high quality surface treatment - not all the advantages of ballscrews. However, it has some disadvantages: high cost and restrictions on the speed of rotation of the screw, if its length is more than 150 cm.
Rack-and-pinion devices provide high speed and accuracy of the work performed, withstand heavy loads, are easy to install and reliable in operation. The error in the transmission of the rack is extremely low. If their size does not fit, then they undergo a fitting operation.
A step-by-step algorithm for manufacturing a household table with a mechanical drive
To make a coordinate table with the simplest, mechanical drive, you must follow the instructions:
- It is necessary to make the central node of the table in the form of a cross from metal profiles 20 x 20 cm (2 mm thick). It should ensure the stability of the entire structure, so all parts are welded.
- Assemble carriages with a stroke of 94 mm on the surface of the finished cross.
- Process the profiles with a file, then insert the M10 nuts into it.
- On the M10 studs, assemble the handles with the bearing assembly.
- Next, you should weld two U-shaped bases from the corner, and then assemble the entire structure on the bolts that were screwed into the previously pressed nuts.
- Wipe all components, as well as moving parts, with lubricant.
- The assembled table must be attached to the bed of the drilling machine.
To ensure that the lubricated structural elements are protected from ingress of chips or other waste during processing of the workpiece, it is advisable to lay plywood between the coordinate table and the machine. The dimensions of the finished manipulator will be 35 x 35 cm, and the product thickness - 6.5 cm. It is desirable that the total length of the guides is about 30 cm.