Epoxy table technology, interesting ideas
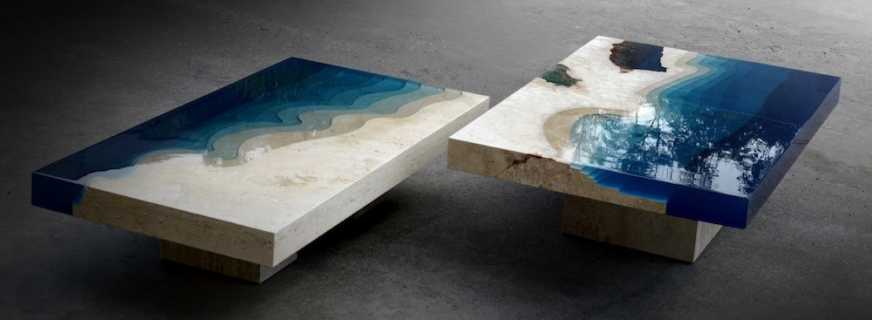
Unusual design solutions are increasingly found in modern apartments. In addition to standard materials, such materials are also used for manufacturing that allow realizing the most interesting ideas. It looks very impressive table made of epoxy resin, which can be done with your own hands. In combination with wood, this material allows you to create real masterpieces.
Content
Design and construction features
Tables made of epoxy resin are characterized by a unique design and can fit into any interior. Most often they are used in kitchens and living rooms, while there are no strict requirements for a style decision. Epoxy is used not only for the manufacture of new products, but also for the restoration of old furniture. Many models are made by combining several materials.
The peculiarity of the resin is that it almost does not shrink after hardening, therefore it retains its original shape for a long time. In addition, it can be decorated in different ways. Resin tables come in several types of designs:
- Combined. In this case, the synthetic material alternates with the elements of wood.
- With the presence of support. Only the top layer is poured with resin. In addition, various decorative elements are used: leaflets, coins, flowers.
- Without the presence of a support. There is only an epoxy. In this way, small coffee tables are made. They are not intended for significant mechanical stress.
The product can be transparent, one-color or combined. Most often used light turquoise, blue shades. Often, the design is equipped with additional lighting or fluorescent powder. Handmade tables have a high cost, but such furniture can be made independently. The advantage of the process is the reduction in the cost of the model. There are other pluses: the ability to show imagination, the restoration of old furniture in an original way.
Epoxy Resin Properties
Epoxy resin is a synthetic oligomer material. In its pure form, it is not used. To obtain a solid fragment, the resin must be polymerized using a hardener. Different proportions of components allow you to create materials with different physical and mechanical properties. Resin has the following qualities:
- strength and resistance to chemicals;
- lack of an unpleasant smell when working with epoxy;
- the polymerization process occurs at a temperature of from -15 to + 80 degrees;
- slight shrinkage after solidification of the material, its stable structure;
- poor moisture permeability;
- high resistance to mechanical damage and abrasive wear;
- lack of need for expensive care.
When using additional protective components, such a table becomes immune to direct sunlight.
The resin also has some disadvantages: when exposed to high temperatures, it is capable of releasing harmful substances. To work with the substance, you must have certain skills and fully comply with the application technology. Such material has a high cost.
Popular modifications
Making an epoxy resin table is a task for a master with a good imagination. In addition to standard pieces of wood, for decoration, you can use luminescent paints or powders, buttons, wine corks, moss, plant leaves, sea stones, cobblestones.
River
A design feature of the river table with epoxy resin is that it is based on the same placement of elements: an insert of the specified material is localized between two pieces of wood. It can be straight or repeat the bends of a tree, wide or narrow, with decorative fragments, islands, pebbles.
The shapes of the countertops here are different: round, oval, rectangular. Interesting options are those in which wood plays the role of a river bank, and resin plays the role of water. You can install these products in the living room and in the kitchen. Looks great model in the office. With the river you can make a coffee table in the style of Provence, country. As for the consumption of material, about 13-14 kg of substance are needed on the river with dimensions of 210 x 15 x 5 cm.
Solid surface
To create a continuous table of liquid glass, the use of the required size is required. Most often, such structures are made without support and do not provide for intensive loading. Countertops of this type are used for the production of coffee or dressing tables. For the manufacture of epoxy resin countertops, the dimensions of which are 100 x 60 x 5 cm, about 30 liters of resin are required.
From slab
Slabs are solid massive slabs of wood or stone. To make such a product at home, a lighter material is taken. The tree is usually a longitudinal cut of the trunk with the remaining knots, bumps along the edges. This will create a unique model.
Often a slab table is made of oak. In this format, you can make a kitchen surface, a design for the living room, study. The thickness of the wood material in this case is from 5 to 15 cm. It should not be glued or have other compounds. To make a table from slabs with medium-sized epoxy resin, about 10 kg of substance will be required.
From cuts
Solid wood tables look very original, rich. No less spectacular look models sawing wood material coated with a solution of epoxy. To fill such a countertop, a minimum of 7 kg of polyester substances is required. This model is great for kitchen, country cottage in the style of eco. No matter which hemp or solid trunk saws are made of, the pattern of each of them will be unique.
Tables of this type have different shapes: round, oval, rectangular and even square. The number of fragments used depends on her choice. The material should be of high quality and the desired diameter. Cracked items are not recommended.
Wireframe selection
The epoxy table, like all other models, consists of a countertop and a support. For their manufacture can be used completely different materials. You can choose the appropriate type of structure based on its purpose.
Countertop
When making a table of wood and epoxy, you must choose which elements the upper part will consist of. Looks great as a flooded array, and its individual pieces. If the material is soft, a thinner resin should be used.
To make a wooden table with epoxy, you can use transversely cut boards, branches, wood with recesses, large saw cuts of a tree. Moreover, the grade and hardness of the material in one product may vary. It is more difficult to work with unprocessed fragments, but the product is more beautiful. If the structure is made of a solid board, then the top layer is filled with resin instead of varnishing the surface.
Transparent countertops are also popular. The technology of their manufacture provides for the creation of molds from plywood or glass. The filler can be completely different: stone filling, artificial pearls, sand, shells, cones.
It looks interesting version of the table made of epoxy resin with volumetric images or dioramas inside. A luminous model can be entered into any interior, making the atmosphere more romantic. You can also build an epoxy table from several layers of hardened material by gluing them together.
Base
Most often, the legs on which the tables are made of epoxy resin are made of wood or metal. Each material has its own characteristics. You need to choose it based on the operating parameters of the table and the overall interior.
A type | Specifications |
Wooden | They look natural, stylish, thorough. They are durable and practical. For the manufacture of supports it is better to take oak, beech or larch wood. They provide maximum stability to the product; they are great for the classic style of interior design. |
Metal | Even if you need to make a table from solid wood with epoxy resin, such legs will become a stable support. The range of materials is wider: steel, cast iron, aluminum. Painting the supports is optional. If the metal is used in domestic conditions, then it does not require additional processing. Iron is more durable than wood, remains resistant to mechanical damage. |
As for the shape, the base can be made in the form of separate legs, square or rectangular frames. In round models, one support made of wood or metal and fixed in the center looks amazing.
Work technology
For the manufacture of the table, epoxy and wood must be correctly selected. Do not give preference to too cheap formulations, as they quickly become cloudy and yellow. The best type of epoxy on the table is CHS Epoxy 520. It is usually sold immediately with a hardener. Mix these substances in the proportions specified in the instructions.
To prepare the solution, 2 containers are required. The resin is kneaded first. If it is necessary to change its color, color is added to the substance. After that, the mixture is heated to 30 degrees and thoroughly mixed. Now the right amount of hardener is added. The mass is mixed until smooth. If bubbles appeared in it, then they should be blown with a hairdryer.
To make tables of wood and epoxy, you need to achieve the correct density of the composition. The final result depends on it. There are such degrees of viscosity:
- Liquid. The mass drains easily from the stick. It penetrates the wood well, penetrating into all the recesses, pores, corners.
- Semi-fluid. This form of composition is used when pouring a round table of epoxy resin and wood.It is also used for the manufacture of decorative parts.
- Thick. It is not suitable for pouring. Such a composition is used if you need to restore an oak table. Another such consistency is used for the manufacture of jewelry.
Before starting the main work, primary processing takes place without the use of an auxiliary box. It is necessary to fill in all the cracks and holes, then these areas are heated to leave air bubbles. After drying, these areas must be sanded so that they are flush with the surface of the board. Next, you need to cover the entire board with a thin resin layer, driving the air out of the pores, and thoroughly dry it.
Do-it-yourself preparation of a mold is required to make a table from epoxy resin. To this end, glass is usually used, which must be well cleaned and treated with a degreaser. It is necessary to pay attention to the presence of chips, cracks, quality of joints.
It is not difficult to make a table from epoxy with your own hands, it is important to follow the technology. The substance layer should not exceed 5-6 mm. Pour the product with a thin stream with a stick. A spatula is used to level the resin. To remove air bubbles, you need to pierce them with a needle or blow with a hairdryer. The finished table of solid wood and epoxy should be covered with polyethylene, to prevent dust and debris.
After the product hardens, it must be sanded, polished and varnished. Coarse abrasive for a table made of epoxy resin must not be used. Grinding is done slowly, and water is periodically poured onto the surface so that it does not overheat. After the completion of the process, the table is varnished.
Since you need to make the table with epoxy resin technologically correct, it is important to observe the nuances of working with the composition. Resin quickly solidifies in a warm room. Top layer can not be heated, as it is deformed. In addition, there are other features:
- during the hardening of the layer, direct sunlight should not be allowed to fall on it, since the resin will turn yellow;
- when working with the composition, use protective equipment;
- Knead the resin slowly.
If the master is engaged in pouring in the winter, do not leave a slab table in the cold, otherwise the resin will delaminate. After drying, the product can release toxins, so you need to apply a protective varnish on it.
To work with filler materials, you need to correctly calculate how much raw material is needed. Here you should use this formula: V = A (length) x B (width) x C (thickness). Since the resin is denser than water, it is necessary to take into account the coefficient and use this formula: V x 1.1. The standard consumption of a substance per 1 square meter of area is 1.1 liters, if the layer thickness is 1 mm.
Step-by-step master class
Now you can consider how to make an epoxy table yourself. Each model has its own manufacturing features. Initially, the tool and material are prepared.
Coffe table with river
For production, it is better to use oak or elm. Soft breeds are not recommended. Master class on creating a coffee table:
- Preparation sawed. It must be well polished.
- Making molds. It should have sides with tight joints.
- Spreading fragments of saw cut. Since the table is made with a river, a niche of a given shape and width is left between the parts of the wood.
- Tinting and pouring resin.
- The manufacture of underframes.
The structure must be covered with polyethylene and allowed to solidify. After 2-3 hours, the sides can be removed. Next, the product is finished.
Slab Dining
Here you need to make a drawing indicating the exact size of the countertop. For such a model, you also need to prepare a form. The work is performed step by step:
- A suitable piece of wood is selected.
- Since the product is made of slab wood, the material must be cleaned of dust, rot fragments.
- Making molds and laying material.
- Cooking and pouring resin.
- Production and fixation of legs.
If several slabs are used, resin leakage must be avoided. After solidification, the excess epoxy must be removed with a grinder. Lastly, the surface is coated with a colorless varnish.
From solid with luminescent paint
To work, you need an epoxy, luminous paint and a board, which should be cracked. It will take 3 fragments of a given length. The following work stages are carried out:
- The formation of countertops. The boards are glued together and left overnight to dry.
- Cleaning cracks from dust and debris.
- Grinding wood surface. Before pouring resin with an acrylic film and adhesive tape, it is necessary to protect the side and end parts of the array.
- Epoxy preparation. At this stage, photoluminescent dye is added: 100 g of dye is used per 2 liters of resin.
- Filling cracks on the surface of the tree. The procedure is carried out at least 10 times at regular intervals. After that, the array should dry overnight.
- Elimination of film, adhesive tape, tar residues.
- Grinding the surface and applying polyurethane paint with a glossy sheen.
Lastly, the legs are fastened to the countertop using anchor plates and bolts.
To make the table glow, it must be put in a well-lit place. Only in this case will the surface absorb enough light.
Updating an old table with epoxy
Even if the table has deteriorated over time and under the influence of negative factors, it can not only be updated, but also made into an original piece of furniture. For decoration, you can use photographs, buttons or coins. The work includes the following stages:
- Elimination of rotten and damaged areas, old paint. It is necessary to dry the surface thoroughly.
- Laying decorative elements. If they are light, then it is better to stick them to the base, otherwise they may surface.
- Application of resin. The procedure is repeated several times with an interval of 2-3 days.
The dried layer should be sanded and varnished. Restoring or making epoxy tables is not a technologically simple process. But subject to all the nuances of work, you can independently create a real masterpiece.