Mirror manufacturing technology, how to make a product yourself
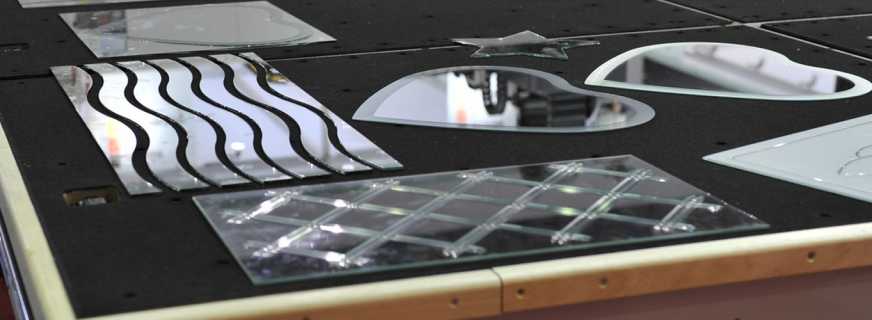
Mirrors firmly entered our life, making it more interesting and informative. It is thanks to them that people get the opportunity to study their appearance in detail, visually expand the space, fill the room with additional light and a special aura. Once again, looking at his reflection, sooner or later, any person thinks how to make a mirror and why it is endowed with a magical nature. An interesting history of creating reflective surfaces, which originates from the moment of the development of civilization, will help to understand these issues.
Content
Basic design
The mirror is a glass surface of varying degrees of purity, which is connected to a layer of reflective spraying - an amalgam. Surprisingly, the production of interior items familiar to a modern person began not so long ago, although reflective surfaces were often found during excavations of ancient palaces, burials of royal people, aristocrats, and noble people. Often these items were exquisitely decorated with precious stones, the handles of some items were made of ivory. Today it’s hard to imagine that such a familiar household item could once be an unacceptable luxury for most people.
In 1279, Franciscan John Pekam described how to make a mirror by treating glass with a thin layer of lead. This method of obtaining a reflective surface was difficult and even dangerous, since it involved the use of mercury. The product itself was not of high quality, had a muddy surface. Despite all the shortcomings, it was this mirror production technology that was used without significant changes until almost 1835.
The release of modern accessories based on glass and reflective coating was started only after the industrial revolution. Since that time, production technology has not been substantially changed. Two methods for manufacturing mirrors are now popular:
- spraying on the glass surface aluminum, titanium, as well as other metals and alloys;
- production of products from a solution of silver, which is fixed with a layer of copper or special chemicals.
Another way to obtain a flexible, unbreakable surface is the deposition of metallic silver on a celluloid.
In ancient times, ponds and polished metal plates — copper, tin, bronze, platinum, steel, and even gold discs — which were polished with gems or semi-precious stones with a high degree of reflectivity, acted as mirrors.
The technology of manufacturing a mirror cloth
The production of mirrors in the modern world, in comparison with antiquity, is much safer, but no less interesting. Today, products are created by combining two components - polished glass and amalgam. Typically, both components are produced in the same factory. The final product complies with all standards and requirements, since the production has all the required ingredients and raw materials. But it happens that glass is produced to order by a company manufacturing mirrors in another organization. The main requirement for such products is the highest degree of purification, they should not have impurities, since any particles in the composition change the quality of reflection.
The raw materials for the production of glass are subjected to thorough cleaning in several steps and then sent to remelting. What mirrors are made of:
- sand quartz;
- dolomite;
- soda;
- glass waste (fragments);
- coal.
Before you make a mirror, you need to prepare the composition for the reflective layer. As a rule, silver oxide is used for this purpose. Typically, silver products darken when combined with oxygen, but the technology of manufacturing a mirror provides for the preservation of the original properties of a noble metal. As a result, the finished product has a reflective surface.
For manufacturing, a base in the form of an even glass sheet is required. To obtain it, all components are subjected to grinding, after they are mixed until a homogeneous powder - glass mixture. Then, using a conveyor, the raw materials are sent to the furnace, where the liquid mass is obtained as a result of melting.
To obtain the smoothest surface, baking is carried out at a temperature of more than 1500 degrees. The result of all the manipulations is a 3 x 4 meter glass sheet with a thickness of about 4 mm. After cooling, it is sliced and checked for defects.
To obtain a reflective surface, it is necessary to apply a chemical composition to the workpiece, adhering to special technology. The glass plane is polished to perfect evenness, then washed, dried, and then coated with a solution. Within 20 seconds, the aldehydes are oxidized with an ammonia solution of silver oxide. When the reaction is complete and the composition dries, a mirror surface appears on the back of the made canvases.
To produce a reflective fabric in another way, a layer of a metal alloy of titanium and aluminum is applied to a perfectly flat glass plane. Next, the mirror cloth is checked for marriage. A special dark green paint is applied to the reflective layer to protect it from damage. In the final stage, the created products are sent for packaging and delivery to the customer.
Variety of products
There is currently no shortage of mirrors, and the cost of these products is quite affordable. People use all kinds of variations of the reflective surface, among which cosmetic mirrors are distinguished:
- Road. In the manufacture of such models, shock protection is provided, and the products themselves are compact in size especially for ease of transportation.
- Pocket. These are models that resemble ladies' powder box. They provide a miniature size, usually they need to be folded and closed before storing in a pocket or bag.
- Shaving mirrors. The products are equipped with a special stand and are sometimes equipped with a backlight for the convenience of the owner.
- Handbags. Accessories manufacturers insert them into the frame for convenience, with their help the owner will be able to control her appearance in any conditions.
Interior mirrors are represented by no less extensive assortment:
- wall-mounted ones have a wide variety of shapes - from classic geometric shapes to bizarre configurations;
- desktop equipped with a stand to place the product on the table, window sill;
- mirror panels are hung on the walls, they are available in different models and are more like decoration than a functional object;
- tile with a reflective surface is used in the design of the room to expand the space.
The edge of the mirror canvas is made out in different ways:
- Facet - a technology that involves ridding the canvas of sharp edges. Edge grinding using this method is used in the manufacture of furniture, equipment for trade and exhibition halls, in the design of stands, where mirrors with an open edge are provided.
- Euro edge - professional edge processing and mirror polishing. This technology is used in furniture production, for countertops, partitions, steps from a mirror, glass doors and other things.
- Polishing removes coarse areas at the edges of the mirror. It is made around the perimeter of the canvas until the edge of the product becomes transparent. Polishing is used after cutting and grinding the mirror.
- The raw edge of the mirror remains after cutting. Such a canvas often serves as a decorative element in the design of the interior.
The ends of the product are processed so that the mirror can be used safely, without the risk of injury by sharp edges.
How to create safe mirrors
Safety mirrors are made of different materials. There are surfaces made of acrylic, special unbreakable glass, in addition, there are mirror plates based on plastic from several layers.
Acrylic-based safety mirrors are used for home use, in kindergartens, entertainment centers and game rooms. Such accessories are made to order. They do not break, are light in weight, do not contain harmful substances and clearly convey the image. Similar products can produce in any form. Mirror acrylic works well. It is not afraid of moisture, because it can be used in bathrooms, pools. This is one of the best and safest options for children to use.
For the child’s room, it is necessary to choose mirrors that do not have sharp edges. The surface must be firmly fixed. It is better if the mirror cloth is based on plastic. If this could not be found, you can use a special interior film that covers the mirror surface, and in case of damage it will hold the fragments, preventing them from crumbling.
How to make it yourself
Surely many people thought about how to make a mirror of simple raw materials with their own hands, without having numerous special equipment. At home, the safest and easiest way is to use a thin metal sheet of “paper”. To make a mirror of foil, the following materials will be required:
- the thinnest sheet of raw materials;
- frame;
- glass;
- degreasing alcohol;
- Scotch.
How to make a mirror with your own hands step by step:
- Degrease the glass surface thoroughly.
- Apply foil to the treated surface and carefully fix along the edges with tape.
- Lock the structure with a frame.
After making the mirror at home, its frame can be decorated to your liking.
What is a signal mirror and how to make it
The signal mirror can be made of glass or metal. The second option is a plate polished on one side. At its center is a hole in the shape of a circle, slightly larger than a match head. It is on him that it is necessary to catch a "bunny" to give a signal.
The glass device consists of two interconnected surfaces, mirror and matte. Both are designed to give an alarm. At the same time, they can be used to give a signal during the day, at night, in the full moon, as well as in fog.
A simple signal canvas can be made independently.To make a mirror at home, you will need a metal plate the size of a regular book. It must be polished, in which case the signal will be visible further, after which it is necessary to punch a hole in the center whose diameter is 57 mm. The simplest signal construction is ready, it’s just hard to learn how to use it, it’s impossible to do without numerous trainings.